Heat conductive and exchanger coating series
To improve the protection of a heat exchanger and its tube, CP Phenolics offers a specially developed heat conductive coating series. This coating prevents corrosion, fouling, and incrustation in the tubes. Consequently, by applying the coating on a heat exchanger tube, optimal protection is guaranteed, and operational costs are reduced. The heat conductivity remains constant with the result of better efficiency and allows for a simple cleaning process.
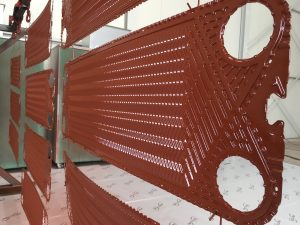
Coated plateheatexchanger
Benefits of a coating for a heat exchanger’s shell tube
Treatment a heat exchanger’s shell tube with a CP Phenolics® coating will lead to:
- Low resistance coefficient (maximum flow through the tubes)
- Optimal heat transfer
- High operational reliability
- Extended lifetime of the heat exchanger
Application description
The coating is a thermosetting coating of minimum three layers. Every layer of coating application gets an oven treatment on a different time and temperature schedule. During the final polymerization session, the coating layers cross link with each other on molecular level. Derived from this, the coating offers high-end corrosion protection against all sorts of aggressive substances that lead to deterioration of the heat exchanger tube.
Cost reduction
The aforementioned cases ensure that investment and maintenance costs will be reduced. We therefore recommend not only to provide a protective coating from our heat conductive coating series on new heat exchangers, but also those who are in actual use.
Example case Project BASF
Entry temperature of condensate: 98 – 103 °C, cooling water speed: 0.3 m/sec.
Buy your heat conductive coating at our company
Due to the absence of heat conductive protective coating, there was a reduced heat transfer of more than 60% in 36 months! Do you want to learn more about the protection of our specially developed phenol coating series or powder coating, and how it can increase the life span of a heat exchanger? Or do you want to learn more about our industrial coating services? Then please contact us at +31 (0)182 30 80 30, fill in the contact form, or send an email to info@cpphenolics.nl.